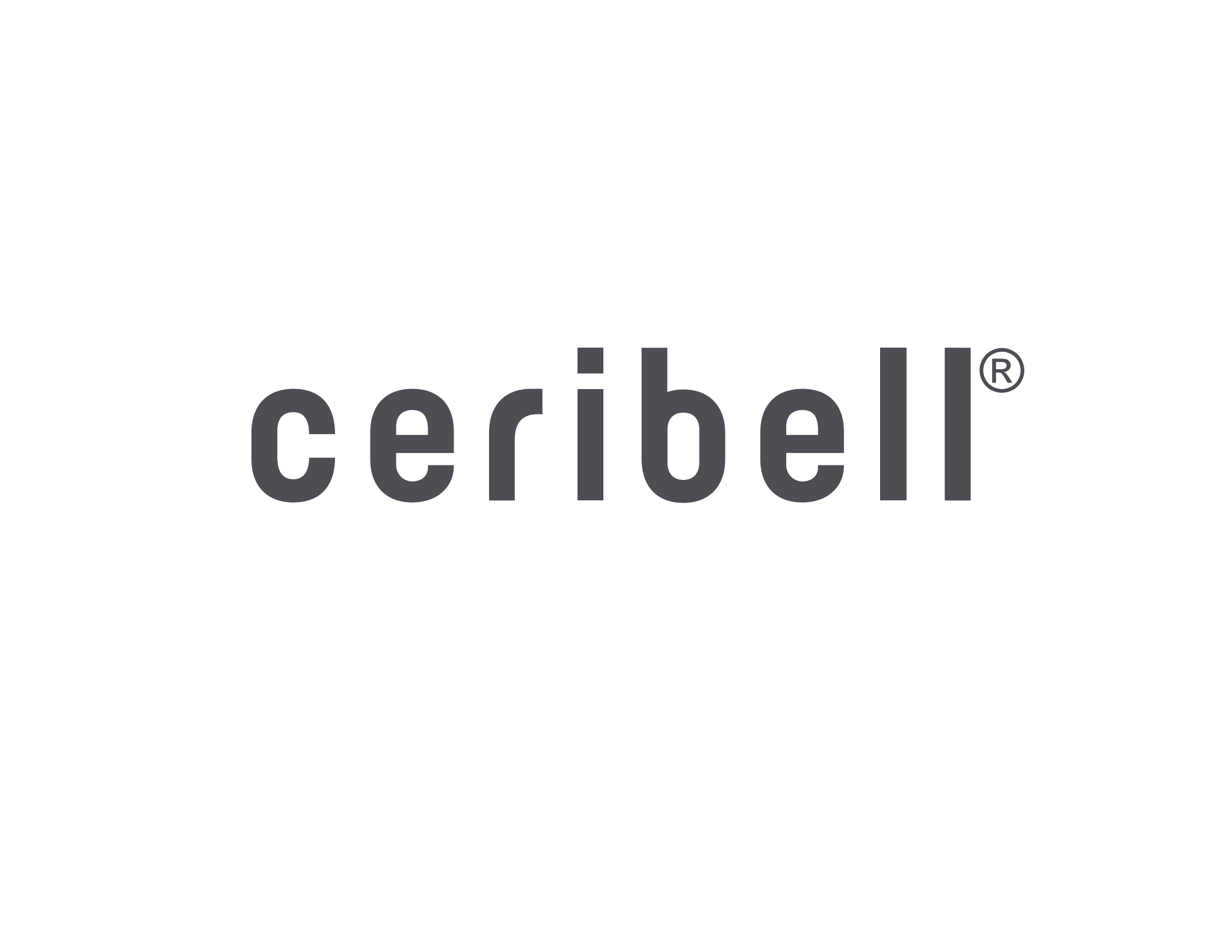
Current openings at Ceribell, Inc
Create a Job Alert
Level-up your career by having opportunities at Ceribell, Inc sent directly to your inbox.
Select...
Select...
28 jobs
Finance and CEO
Job |
---|
VP, FP&A |
Create a Job Alert
Level-up your career by having opportunities at Ceribell, Inc sent directly to your inbox.
Job |
---|
VP, FP&A |