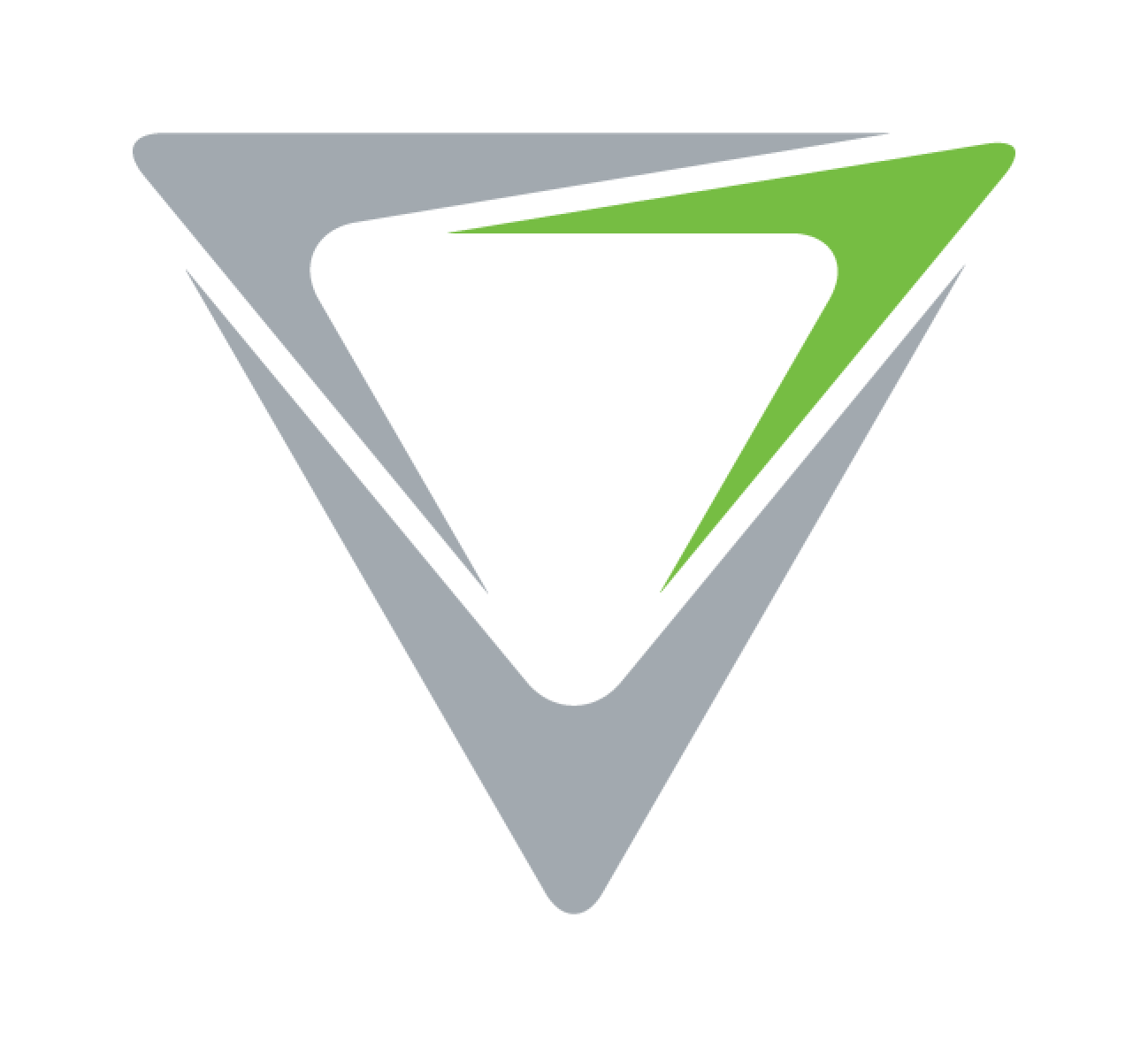
Senior Quality Engineer
Divergent is a technology company that has architected, invented, built, and commercialized an end-to-end factory system called the Divergent Adaptive Production System (DAPS™) that comprehensively uses machine learning to optimally engineer, additively manufacture, and flexibly assemble complex integrated vehicle structures and subsystems. Products created using DAPS are superior in performance, lower in cost, rapidly customizable to meet mission and customer-specific requirements, faster to market, and scalable on demand to high volume production. Divergent is a qualified Tier 1 supplier to global automotive OEMs, and Divergent is now expanding to support mission critical needs in the Aerospace and Defense sector. Join us to be a part of this transformative journey, where your impact will shape the future of technology and production.
Purpose
We are seeking an experienced Senior Quality Engineer to join our growing team. This role will play a critical part in ensuring the quality and reliability of our products and processes, working closely with cross-functional teams to develop innovative solutions for high-precision manufacturing. As a Senior Quality Engineer, you will lead quality control initiatives, implement continuous improvement processes, and help drive the highest standards in production to meet customer and industry expectations.
Key Responsibilities:
Process Improvement and Defect Reduction
• Lead initiatives to improve process efficiency and reduce defects by analyzing quality and production data to identify trends, root causes, and improvement opportunities.
• Implement robust process controls and standardize inspection procedures to enhance consistency, prevent recurring quality issues, and improve first-pass yield.
Inspection Effectiveness and Quality Controls
• Optimize inspection strategies by leveraging advanced tools and techniques, including CMM programming, to balance precision with efficiency.
• Establish and maintain inspection criteria and acceptance standards aligned with customer requirements and industry best practices.
• Ensure inspection methods meet capability requirements through studies like Gage R&R and Cpk analyses.
Customer Engagement and Quality Deliverables
• Quality liasion for customers, managing audits, addressing quality concerns, and ensuring timely resolution of issues.
• Prepare and deliver required quality documentation, including PPAP, FAIR, and other customer-specific deliverables, while facilitating customer reviews and audits.
• Collaborate with customers to clarify quality requirements and maintain alignment on deliverables and expectations.
Nonconformance and Corrective Action
• Manage nonconformance activities, including root cause analysis, corrective/preventive actions, and Material Review Board (MRB) processes.
• Track and analyze nonconformance trends to drive targeted quality improvements and reduce defect recurrence.
Data Analysis and Reporting
• Monitor key performance indicators (KPIs), such as yield, defect rates, and on-time delivery, to identify improvement areas
• Develop dashboards and reports to provide real-time visibility into quality performance and share actionable insights with stakeholders.
Quality Planning and Deployment
• Develop and implement scalable quality control plans and deploy new inspection technologies to align with company objectives and customer expectations.
• Support process validation for new or modified manufacturing processes, ensuring readiness and compliance.
Cross-functional Collaboration and Leadership
• Collaborate with cross-functional teams to integrate quality requirements into product and process development and support new product introductions (NPI).
• Mentor quality team members on best practices for inspection, data analysis, and process control while driving cross-functional problem-solving initiatives.
• Perform any other support functions as directed by Quality Management
Basic Qualifications
• Demonstrated experience leading quality initiatives focused on process improvement, defect reduction, and inspection optimization in manufacturing environments.
• Proficiency in implementing and managing tools such as PPAP, FMEA, and root cause analysis (RCA) to resolve quality issues and improve processes.
• Knowledge of advanced inspection methods and tools, including CMM programming, Gage R&R, and sampling techniques, with a focus on effectiveness and efficiency.
• Strong analytical skills with the ability to interpret data, identify trends, and drive data-informed decisions to improve yield and reduce defects.
• Proven ability to collaborate with cross-functional teams, customers, and suppliers to ensure quality standards and customer expectations are met.
• Clear communication and documentation skills to effectively present quality metrics, deliverables, and insights to stakeholders.
Preferred Qualifications
• Bachelor’s degree in Engineering (Mechanical, Industrial, Electrical, or related field) or equivalent experience in a quality-focused role.
• Experience in regulated industries such as automotive, aerospace, or defense with familiarity in standards like AS9100, ISO 9001, or IATF 16949.
• Hands-on experience with Production Part Approval Process (PPAP) documentation and customer engagement for quality deliverables.
• Expertise in statistical process control (SPC) and process capability analysis (Cpk) for monitoring and improving production processes.
• Certification in Six Sigma (Green Belt or higher) or ASQ Certified Quality Engineer (CQE).
• Familiarity with advanced manufacturing technologies such as additive manufacturing or automated inspection systems
Work Environment
• This role is based in a dynamic manufacturing environment with exposure to production areas, quality & material labs, and office settings.
• Some travel may be required for customer audits, supplier evaluations, or off-site quality initiatives (up to 20%).
• Position requires frequent standing, walking, or light lifting up to 25 pounds.
Pay Range
$122,400 - $168,300 USD
- Holistic Compensation Package: Enjoy a world-class compensation package that includes a competitive salary, equity plan, and discretionary results-based incentive bonus opportunities, ensuring you're truly valued for your contributions.
- Wellness and Time Off: Embrace a healthy lifestyle with paid vacation, sick time, and company holidays, including a year-end shutdown to recharge. We support growing families with paid parental leave, recognizing the importance of bonding time.
- Comprehensive Health and Wellness: Prioritize your well-being with our comprehensive health and wellness benefits, offering both HMO and Premium PPO options. Additionally, benefit from company-sponsored life insurance and short and long-term disability coverage for peace of mind.
- Investment in Growth: We're committed to your professional development. Take advantage of reimbursement opportunities for learning and development initiatives, empowering you to continuously expand your skill set and reach peak performance.
- Inclusive and Collaborative Environment: Join our inclusive, collaborative, and dynamic work environment within a fast-paced, mission-driven company. Together, we're disrupting the traditional manufacturing industry, embracing diversity, and fostering innovation to reduce our footprint by integrating people and technology.
Apply for this job
*
indicates a required field