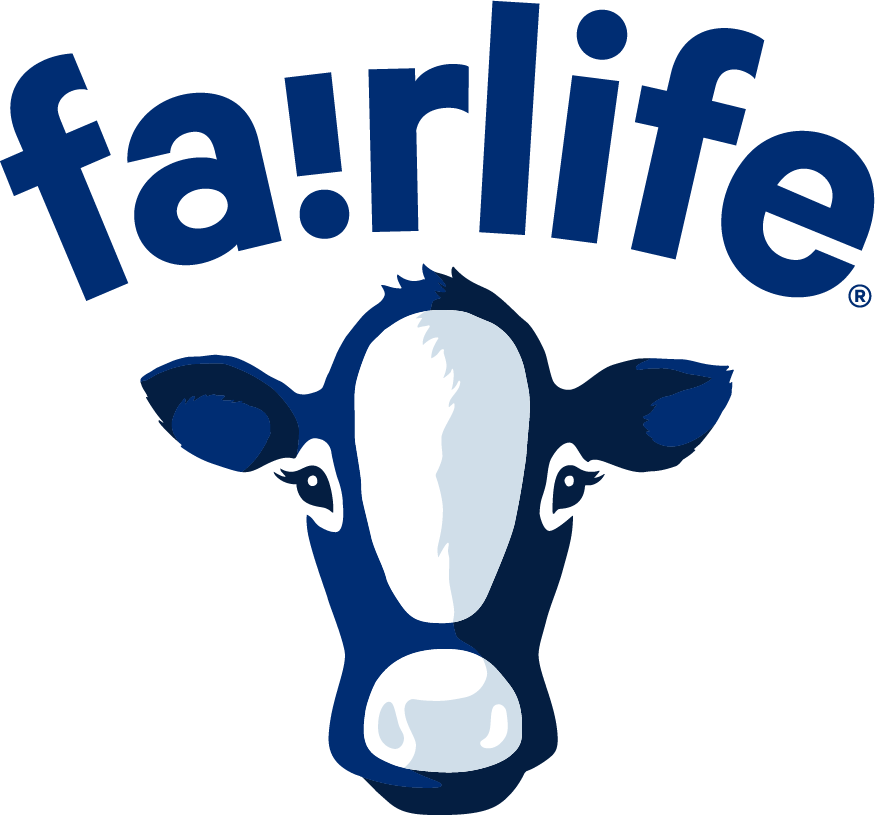
Sr. Packaging Manager
fairlife, LLC is a Chicago-based nutrition company that creates great-tasting, nutrition-rich and dairy products to nourish consumers.
With nearly $3B in annual retail sales, fairlife’s portfolio of delicious, lactose-free, real dairy products includes: fairlife® ultra-filtered milk; Core Power® High Protein Shakes, a sports nutrition drink to support post-workout recovery; fairlife® nutrition plan™, a nutrition shake to support the journey to better health.
A wholly owned subsidiary of The Coca-Cola company, fairlife, LLC has been recognized by both Fast Company and Nielsen for its industry leading innovation.
To learn more about fairlife and its complete line of products, please visit fairlife.com.
job purpose:
The Senior Packaging Manager works in partnership with the Off Shift Packaging Manager and the Director of Operations, leading our 24/7 packaging hall operations in Goodyear, AZ. This role leads and supports a staff of four 12-hour shifts including the department’s supervisory team, Senior Leads, as well as our packaging operators working within our filler/blow molder, sleever and variopac/palletizer work cells. The Sr. Packaging Manager drives development of Packaging Department strategy and is responsible for implementation with a focus on building long term capability for the department. The incumbent has the ability to drive or support the design of and is responsible for implementation of programs for human & food safety, engagement, manufacturing excellence, and financial stewardship in a cross-functional environment. This person is critical to setting the agenda and for driving a sound department where favorable results are the norm, and the daily focus is on safety, continuous improvement, engagement and loss elimination.
responsibilities:
- Drives the growth of the department’s capability through a relentless focus on technical, leadership, and systems mastery.
- Has a deep and wide knowledge with change management and experience with transitioning an organization from traditional manufacturing principals to a TPM approach.
- Places a high value on safety, quality, manufacturing fundamentals, and people development which are foundational to the team’s culture, and this permeates all through the organization.
- Owns and drives a culture focused on zero losses through standardization and loss elimination.
- Accountable for the department’s results: meeting production goals, schedule attainment, meeting or exceeding scheduled OEE, deviations, FTT, scrap, CPM, budgetary spend and unit costs.
- Fully responsible to drive a high level of employee engagement for the team.
- Utilizes a CI and lean approach and tool set to solve and eliminate issues from recurrence.
- Oversees planning, execution, follow ups and corrective actions for all change-over activities and non-routine operational and maintenance actions.
- Has the leadership ability to back up the Director of Operations when this person is out of the plant for days at a time.
- Works to establish and cascade relevant Key Performance Indicators throughout the department and ensures timely reporting to peers, team members, and senior leaders.
- Reviews inventories and production plans daily with the site planning team, coordinating schedule demands with staff and product movement personnel.
- Supports key capital projects and commercialization projects relevant to the packaging department.
- Reviews all nonconforming products and materials with Quality Assurance and Packaging Engineering Team.
- Ensures compliance with GMP’s, sanitation, food safety and employee safety.
- Partners with our Maintenance team to ensure all equipment stays in reliable working condition.
- Manages team members across a 24/7 operation.
- Performs other duties as necessary.
skills/qualifications required:
- Required:
- Bachelor’s degree in industrial engineering, mechanical engineering, brewing engineering, operations management, or other quantitative discipline with a demonstrated and proven knowledge of fluid dynamics in a beverage manufacturing environment, and
- At least five (5) years in manufacturing leadership. Dairy industry with both ESL and Aseptic experience or Brewing Industry experience with carbonated packaging across bottles, cans and kegs in a high-speed and high-volume environment is required with a demonstrated record of increasing responsibility, which must include at least two (2) years as a Shift Supervisor and at least one (1) year as a manager with proven favorable results, or
- At least eight (8) years of beverage industry manufacturing experience. Dairy industry with both ESL and Aseptic experience is highly preferred with a demonstrated record of increasing responsibility, which must include at least four (4) years as Shift Supervisor and (1) year as a Manager with demonstrated positive results for repeatable and reproducible schedule attainment and throughput.
- A self-starter who is driven by the thrill of continuous improvement daily.
- Organized and methodical thinker.
- Superior communication skills.
- Ability to read and understand P&ID’s.
- Preferred:
- Working knowledge of the regulatory and food safety requirements. PMO, FDA, PCQI, FSMA, CCPs and thermal processing and Preventive Controls
- Continuous Improvement mindset including root cause analysis, strategic planning, Lean, and TPM principals.
- Ability to meet production schedules with shifting priorities.
- Understanding the chemistry of cleaning and CIP/SIP/COP programs. An understanding of 3A guidelines is preferred.
- Strong interpersonal, verbal, and written communication skills.
- Demonstrated success working in a fast-paced, entrepreneurial environment.
food safety requirements:
- Responsible for maintaining critical control points, aseptic requirements, and regulatory standards, at all times.
- Accountable for passing internal Quality and Food Safety program audits.
- Perform all duties necessary to meet Company, Customer and/or Government requirements/standards as prioritized by the Company.
- Ability to initiate action to prevent the occurrence of nonconformities relating to Food Safety and the Quality of the product, processes, quality system, or safety system.
- Identify and record any problems relating to Food Safety and the Quality of the ingredients, processes, quality system, or safety system.
position location: Goodyear, AZ
reports to: Director of Operations
travel requirements: Less than 5%
exempt/nonexempt: Exempt
fairlife, LLC is an equal opportunity employer. We do not discriminate on the basis of race, color, religion, age, sex, national origin, disability status, genetics, protected veteran status, sexual orientation, gender identity or expression, or any other characteristic protected by federal, state or local laws. All qualified applicants and employees will be given equal opportunity. Selection decisions are based on job-related factors.
In addition to its nondiscrimination commitment, the Company will also provide reasonable accommodation of qualified individuals with known disabilities unless doing so would impose an undue hardship on the Company. If you have a disability and would like to request accommodation in order to apply for a position with us, please email careers@fairlife.com.
Apply for this job
*
indicates a required field