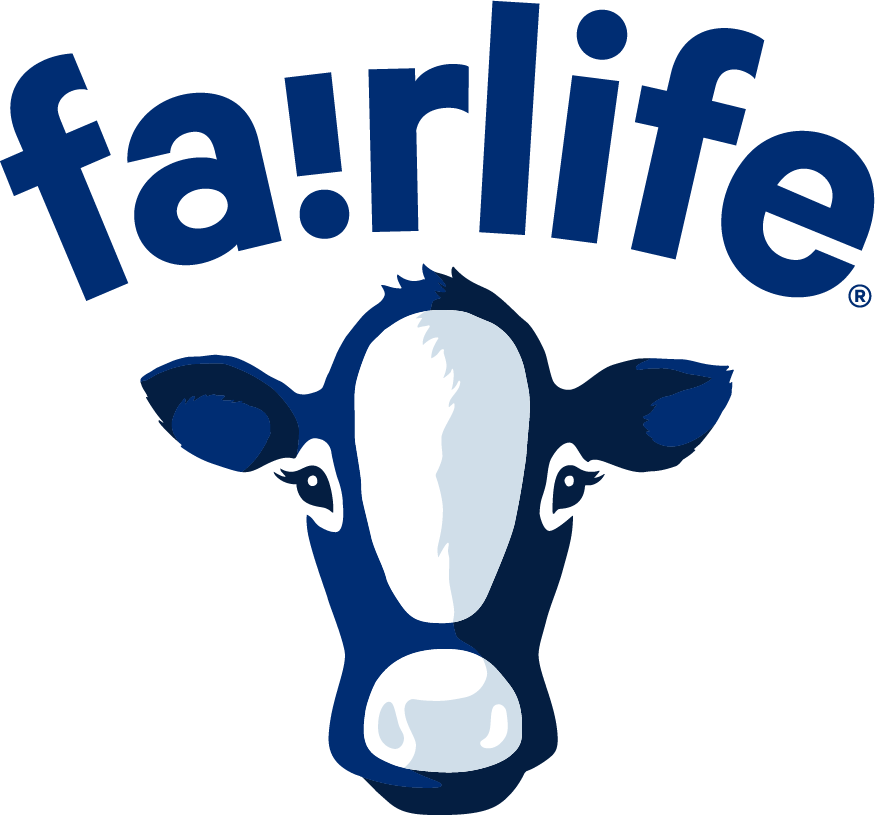
Processing Supervisor - Days
fairlife, LLC is a Chicago-based nutrition company that creates great-tasting, nutrition-rich and dairy products to nourish consumers.
With nearly $3B in annual retail sales, fairlife’s portfolio of delicious, lactose-free, real dairy products includes: fairlife® ultra-filtered milk; Core Power® High Protein Shakes, a sports nutrition drink to support post-workout recovery; fairlife® nutrition plan™, a nutrition shake to support the journey to better health.
A wholly owned subsidiary of The Coca-Cola company, fairlife, LLC has been recognized by both Fast Company and Nielsen for its industry leading innovation.
To learn more about fairlife and its complete line of products, please visit fairlife.com.
job purpose:
This position is responsible for all personnel and equipment within the Processing Department during the scheduled shift. The primary activities include but are not limited to: administration of time and attendance for employees, equipment troubleshooting, operational program execution and development, achieving and tracking production goals, facility safety and quality awareness, and material and inventory tracking and monitoring.
responsibilities:
- Responsible for operator supervision, training, and reporting on the daily operation of the processing equipment and these roles which consist of the UHTs, Membranes, Separators, HTST, Batching equipment and ancillary equipment needed for operations and cleaning.
- Manage production lines through all aspects of schedule: production, sanitation, and production changeovers including production raw fluid planning.
- Be Audit Ready: Have floors and drains cleaned as needed, have recording charts in proper condition and check state seals on equipment, inform management as needed.
- Complete and Audit MSS, CL and CIL tasks on the shift.
- Ability to create shift schedules.
- Inform other departments of necessary changes or run conditions and report to Processing Manager any problems encountered, and then follow any further instruction from management.
- Check tanks and equipment to ensure proper CIP.
- Ensure Processing equipment is being maintained in perfect condition by maintenance. Ensure PM’s and work orders are being written and executed by working closely with the maintenance department personnel.
- Maintain inventory of supplies, of assigned items.
- Take inventory of consumables supplies daily ensuring that we have sufficient quantities.
- Responsible for department performance during shift.
- Responsible to handle/escalate any safety concerns that arise during shift including but not limited to: identifying and reporting potential hazards, reporting near misses/incidents, acting as a first responder if trained or notifying first responder if needed, altering plans to mitigate risks
- Manage violations of company policies, procedures, and working rules through 1 on 1 coachings or reporting to appropriate manager.
- Follow all safety and working rules.
- Perform other duties as assigned by management.
- Must be able to read and interpret equipment drawings and P&ID’s. Specifically, for fluid processing equipment and processing equipment.
- Ability to create raw equipment CIP game plan during the shift.
- Responsible of shift escalation protocol process.
- Responsible for shift losses including CAPA or RCA completion.
- Ability to create production fluid plan schedule and managing the consumption levels during the shift.
- Ability to create SOP and training for team members.
skills/qualifications required:
- A Bachelor’s Degree in a related discipline is preferred or six years of experience in a leadership role; or an equivalent combination of education and experience are required.
- Ability to handle ambiguity and work in a fast paced, entrepreneurial environment
food safety requirements:
- Notify supervision of any repairs or adjustments that are required that may affect product quality or food safety.
- Understand, observe, and comply with the handling and usage of the color-coded container policy while in the Production Areas.
- Perform all duties necessary to meet Company, Customer and/or Government requirements/standards as prioritized by the Company.
- Ability to initiate action to prevent the occurrence of nonconformities relating to Food Safety and the Quality of the product, processes, quality system, or safety system.
- Identify and record any problems relating to Food Safety and the Quality of the ingredients, processes, quality system, or safety system.
- Control further processing or delivery of nonconforming product in terms of Food Safety and Quality issues until the deficiency or unsatisfactory condition has been corrected.
- In the event of absence, another employee with the same skill level will assume the duties and responsibilities as required.
- Safety Sensitive position
position location: Goodyear, AZ
reports to: Processing Manager
travel requirements: Less than 5%
exempt/nonexempt: Exempt
fairlife, LLC is an equal opportunity employer. We do not discriminate on the basis of race, color, religion, age, sex, national origin, disability status, genetics, protected veteran status, sexual orientation, gender identity or expression, or any other characteristic protected by federal, state or local laws. All qualified applicants and employees will be given equal opportunity. Selection decisions are based on job-related factors.
In addition to its nondiscrimination commitment, the Company will also provide reasonable accommodation of qualified individuals with known disabilities unless doing so would impose an undue hardship on the Company. If you have a disability and would like to request accommodation in order to apply for a position with us, please email careers@fairlife.com.
Apply for this job
*
indicates a required field