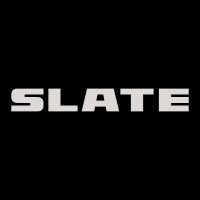
Manufacturing Quality Engineer – Incoming Quality
ABOUT Slate
Slate is a new company that is exploring development in the electric vehicle space.
Who we are looking for:
Slate is looking for a dynamic, experienced Manufacturing Quality Engineer to join our growing team. The position will primarily focus on new products and process development and will play a pivotal role in ensuring a safe and successful launch. The role will utilize core quality skills and tools to manufacture and deliver the highest quality products within our various manufacturing processes. The expectation will be to work closely with internal and external partners to ensure we exceed customers’ expectations.
Applicants must be authorized to work for any employer in the U.S. We are unable to financially sponsor or take over sponsorship of an employment Visa for this opportunity currently
What you get to do:
- Approve PPAP (Production Part Approval Process) Submissions: Review and approve PPAP submissions from suppliers to ensure compliance with quality standards and specifications per inspection plans and requirements.
- Follow Up on Supplier Corrective Actions: Monitor and ensure timely resolution of issues identified in supplier corrective actions.
- Support Problem-Solving Activities: Assist in problem-solving activities related to supplier quality, providing expertise and guidance.
- Provide Production Line Support: Offer support for any supplier quality issues that arise on the production line, ensuring minimal disruption, communicating to the appropriate quality engineer and design responsible engineer.
- Conduct Supplier Capability Assessments: Evaluate supplier capabilities and manage certifications to ensure they meet required regulatory standards.
- Coordinate Incoming Inspection Processes: Oversee incoming inspection processes to ensure supplier compliance with quality requirements.
- Provide part inspection support for incoming inspection for new products, launches, and builds.
- Implement Supplier Performance Strategies: Develop and maintain supplier performance strategies and scorecards to track and improve supplier performance from the launch processes.
- Collaborate with Supplier quality: Work with supplier quality to develop and implement improvement strategies, fostering strong partnerships.
- Conduct Internal Audits: Perform internal audits and monitor key performance indicators (KPIs) such as scrap rates and supplier performance and issue Quality Failure Reports.
- Manage Obsolete Materials: Ensure obsolete materials are managed and aligned with production needs to prevent mixing with active materials during the launch process.
- Collaborate Cross-Functionally: Work with various teams to ensure quality requirements are developed and seamlessly integrated into the manufacturing process.
- Maintain Quality Documentation: Develop and maintain essential quality documentation, including control plans, inspection procedures, and quality manuals.
- Risk Minimization: Utilize risk assessment tools to minimize risks and verify the robustness of detection and prevention systems for special characteristics.
- Support FMEA Development: Assist in the development and maintenance of Failure Modes and Effects Analysis (FMEA).
- Provide Quality Support: Offer quality support to technical and manufacturing teams for supplier issues, driving and supporting daily operations.
- Additional Duties: Perform other duties as assigned.
What you bring to the team:
You will have high integrity, curiosity, resourcefulness, and strive to exhibit a positive and growth mindset. You will feel comfortable operating in a flexible and fast-paced environment with a collaborative approach to achieving goals!
- Bachelor’s degree in engineering, Quality Management, or a related field.
- Minimum of 6+ years of experience in engineering or quality assurance and control within a manufacturing environment.
- Proficiency in quality management systems (QMS) and tools such as Six Sigma, Lean Manufacturing, and Statistical Process Control (SPC).
- Ability to conduct root cause analysis and implement corrective and preventive actions.
- Familiarity with Failure Modes and Effects Analysis (FMEA) and risk assessment tools.
- Strong analytical and problem-solving skills, with the ability to interpret complex data and make data-driven decisions.
- Excellent communication skills, both written and verbal, with the ability to collaborate effectively across cross-functional teams.
- Experience in supplier quality management and the ability to set and monitor quality expectations for incoming materials.
- High attention to detail, especially in maintaining quality documentation.
- Ability to manage multiple projects and priorities simultaneously.
- Ability to adapt to changing priorities and work in a fast-paced environment.
- Willingness to perform additional duties as assigned.
- Strong teamwork and communication skills, a high level of assertiveness, as well as entrepreneurial thinking and goal- and result-oriented decision-making skills.
- Proven track record of engaging and participating in high-performing teams.
- Proficient in the use of commonly applied quality tools and processes in the automotive industry (e.g., AIAG, IATF 16949, MSA, SPC, APQP, PPAP, GD&T etc.).
- Highest level of integrity and the ability to make data-driven decisions.
- Ability to thrive in a dynamic, fast-paced start-up environment.
We want to work with people that reflect the communities in which we operate:
Slate is proud to be an Equal Employment Opportunity and Affirmative Action employer. We do not discriminate based upon race, color, religion, gender, gender identity or expression, sexual orientation, national origin, genetics, disability, age, veteran status, marital status, parental status, cultural background, organizational level, work styles, tenure and life experiences. Or for any other reason.
Slate is committed to providing reasonable accommodations for qualified individuals with disabilities in our job application procedures. If you need assistance or an accommodation due to a disability, you may contact us at recar-talent_acquisition@slate.auto or 813-468-7257.
Apply for this job
*
indicates a required field